How to Use the JLG Analyzer Tool Kit (Part Number 2901443): A Step-by-Step Guide
The JLG Analyzer Tool Kit (Part Number 2901443) is a handheld diagnostic device specifically designed to interface with JLG aerial work platforms, enabling technicians to efficiently diagnose, calibrate, and configure machines.
What’s Included:
- Handheld Analyzer
- Communication Cable
- Instruction Manual
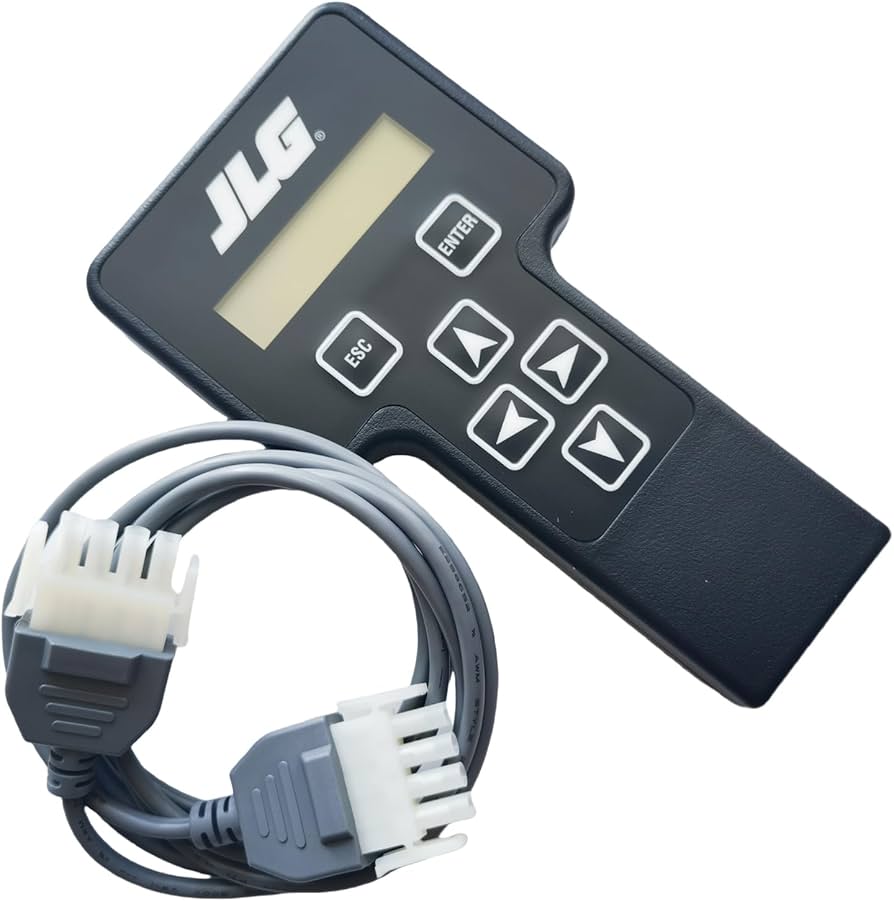
Step-by-Step Instructions:
1. Connecting the Analyzer
- Identify Port: Locate the correct analyzer port on your JLG machine.
- Cable Connection: Connect the analyzer to the port using the supplied four-pin communication cable.
- Power Up: Turn the key switch to the platform or ground position. Ensure emergency stop buttons are disengaged (pulled out) to activate the system.
2. Navigating Menus
- Upon startup, the analyzer displays a menu. Navigate using:
- LEFT/RIGHT Arrow Keys: Cycle through menus.
- ENTER: Select an option.
- ESC: Go back to the previous screen.
- Main menus typically include HELP, DIAGNOSTICS, ACCESS LEVEL, PERSONALITIES, MACHINE SETUP, and CALIBRATIONS.
3. Diagnostics
- Select the DIAGNOSTICS menu to view:
- Platform Load (PLTLOAD)
- Load Cell Data (CELL 1-4)
- System Status (SYSTEM)
- Software Versions (VERSIONS)
4. Changing Access Levels
- Select ACCESS LEVEL.
- Enter the password 33271 to obtain Access Level 1, necessary for adjusting parameters or performing calibrations.
5. Calibration of Load Sensing System (LSS)
- Ensure platform is level (±5 degrees).
- Remove non-permanent items from the platform.
- Navigate to CALIBRATIONS and follow on-screen prompts carefully.
6. Adjusting Machine Settings
- Enter the MACHINE SETUP menu to modify:
- Load settings
- Unit preferences (pounds/kilograms)
- Accessory configurations
Best Practices:
- Perform calibrations every six months or after replacing parts.
- Regularly monitor diagnostic menus to preempt issues.
- Verify all connections to avoid communication errors.
- Always consult your machine’s specific service manual for detailed instructions.
By adhering to this guide, you will optimize your JLG aerial lift’s performance and safety using the Analyzer Tool Kit efficiently.
Aerial Lift Maintenance Aerial Work Platform Diagnostics Certus Certus Equip Electric Scissor Lift JLG 2901443 JLG Access Level 33271 JLG Analyzer Best Practices JLG Analyzer Instructions JLG Analyzer Tool Kit JLG Calibration Guide JLG Diagnostic Tool JLG Diagnostics Menu JLG Equipment Maintenance JLG Load Cell Data JLG Machine Configuration. JLG Machine Setup JLG Platform Load JLG Service Manual JLG Software Versions JLG Tools JLG Troubleshooting Lisfting Equipment Load Sensing System Calibration Maintenance